BuildLabs CEO Punit Chugh has spent the past decade using precision engineering to build a collection of massive, million-dollar beach houses across the East End. But now he’s ready to launch his company’s next iteration: ADU’s and Tiny Homes–Hamptons-Style.
Eastward on Montauk Highway, just past the bustle of Citarella Market and the synergistic charm of the Bridgehampton Inn and Loaves & Fishes Cookshop, sits the offices of BuildLabs, LLC.
It’s hard to miss its headquarters, especially when you’re sitting in peak summer traffic. Its signage tells a story, one driven by technology. The Hamptons builder is testing all the ways AI and machine learning can redefine how luxury homes in the Hamptons are built–be it a 10,000 square-foot mega-mansion or a 250 square-foot accessory dwelling unit (ADU). With builders and homeowners alike constantly under the gun to complete construction by Memorial Day, these advancements could be game-changing for the local Hamptons real estate market—and the local environment.
Buzz around East End businesses typically revolves around celebrity-owned companies, rather than Silicon Valley-like ventures. But BuildLabs, which leverages precision engineering and advanced software technology, is bringing a bit of startup culture to the Hamptons.
After decades as an architect and project manager for billion-dollar infrastructure projects in Australia, Punit Chugh returned to New York figuring out how to eliminate the most common pain points of building because there are many: project delays, change orders, and inflated costs. He started a traditional construction company, while conducting R&D about the best building and engineering practices around the world. “I found myself in Germany touring precision engineering factories focused just on home building,” Chugh says.
By 2013 Chugh and his wife and co-founder, Anjali Gupta, launched BuildLabs, to emphasize their quest to continuously innovate and disrupt traditional construction as we know it. “We bring German engineering and American craftsmanship together to create custom-built homes at scale,” says Chugh. BuildLabs has evolved into a team of 35 and growing with offices spanning Bridgehampton, Germany and India.
Today he touts the company’s ability to build the grandest waterfront gems or countryside compounds in less than a year, versus the typical timeline of two-to-three–but Gupta is quick to clarify, “We’re anything but modular.” Instead, the design-build company relies on a unique on-site, off-site construction methodology, where it manufactures a bulk of its materials and foundational elements at its facility in Germany.
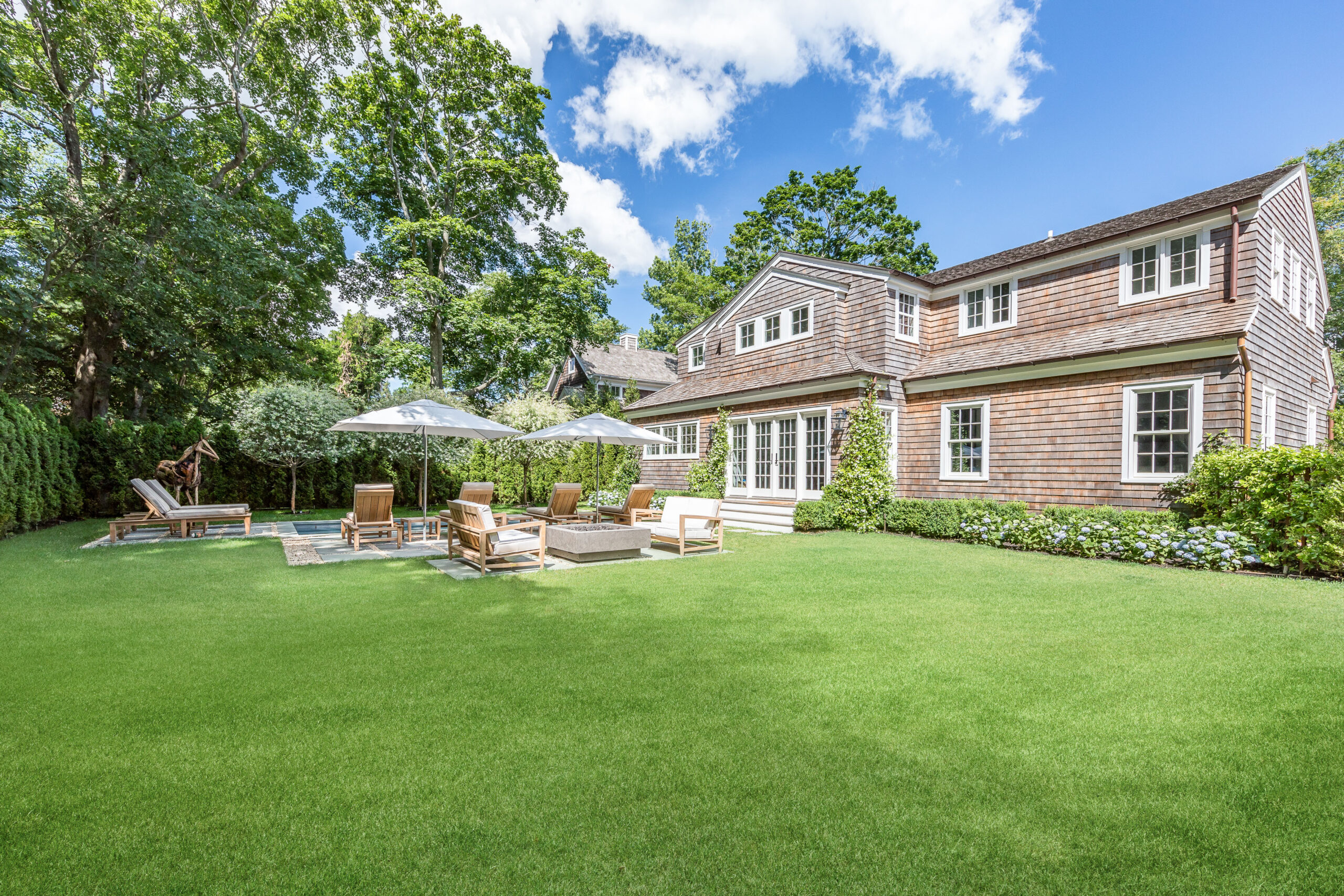
“Our manufacturing lab in Germany is home to the world’s best Computer Numerically Controlled (CNC) machines for timber processing, framing, insulation, down to the windows and doors,” explains Chugh. BuildLabs then directly ships the “building blocks” to the jobsite, where its team assembles the pieces.
“It’s basically like Legos, where it’s a pure play of assembly and execution,” says Chugh. This leads to less timber waste at construction sites, and more importantly to the homeowner, a quicker timeline and less delays. Often teaming up with Sag Harbor-based architect Val Florio, the BuildLabs portfolio features colossal residences, ranging from classic salt-box shingles, to all-glass contemporaries.
In March, BuildLabs wrapped up an 8,000 square-foot residential project in Hampton Bays, which marked a new era of the company’s sole use of strictly blow-in organic cellulose insulation, which are formaldehyde-free and made from recycled natural materials. “We avoid the traditional use of spray foam, which is quite toxic and pretty much banned in most of Europe,” says Chugh.
The company has adopted the use of such eco-materials across its other projects, including a 10,000 square foot home in Watermill, a stunner made of laminated timber wood that could withstand any Hamptons storm and triple-pane glass for better insulation. “The use of these sustainable and effective materials has lasting effects on energy conservation and the homeowners’ health. At BuildLabs, every project is a canvas where aesthetics meet purpose,” says Chugh.
This summer the company broke ground on four projects, including a 12,000 square-foot modern behemoth in Bellport–which is BuildLabs’ largest job yet. The client had a specific request: a 12.5-foot sliding door to seamlessly blend indoor and outdoor living. “The window manufacturers in Germany thought we were crazy, but this is the level of custom detail we reach for clients,” says Chugh.
He says they’ve also disrupted the traditional business model by positioning themselves as a full-service design-build firm that emphasizes cost transparency and accountability. “Ask anyone who’s built a house, there’s always finger pointing among contractors and subcontractors, architects and designers.” Serving as a single point of contact and project management for the entire process, BuildLabs eliminates not only these hiccups, but also the developer’s profit as well, and passes these savings to the homeowner.
The company also relies on software and coding talent to streamline decisions even before an initial consultation, by creating an e-commerce-like experience for custom home building, complete with a high-tech home configurator.
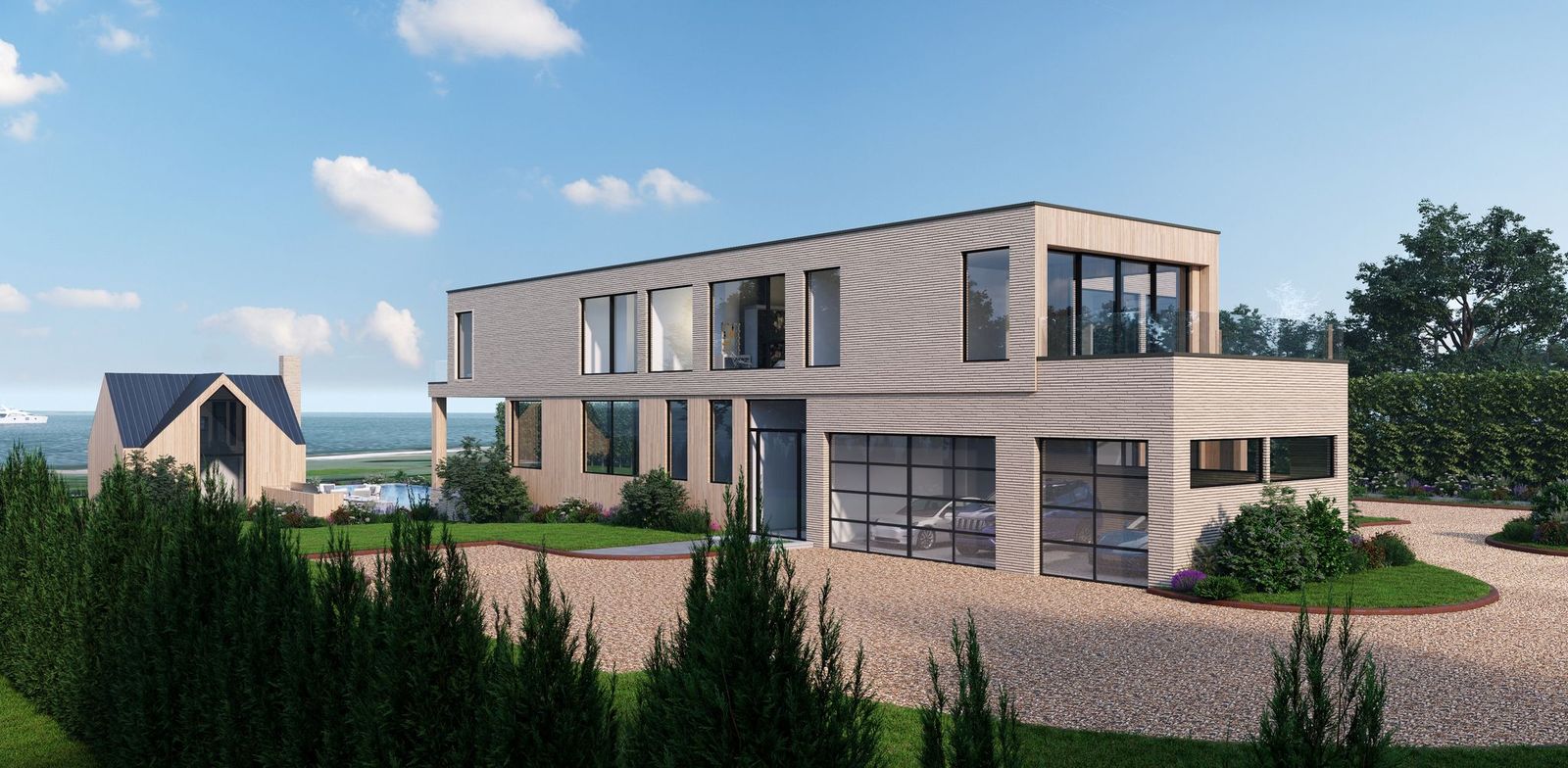
Back at its office in Bridgehampton, which includes an elevated, all-glass standalone conference room, where Chugh and team host a steady pace of client meetings and collaborations with interior designers like Curious Yellow and Cola Studios. The buildout has also served as a showcase for its latest iteration: ADUs. But these aren’t the quirky structures you see on Tiny House Nation on Netflix.
“Ever since we built this, we are getting more walk-ins asking about smaller, practical projects than bigger mansions,” says Chugh. “People come in saying this would look cool on our property, maybe we can turn it into a showroom for our cars or a yoga studio.”
It got Chugh thinking that the BuildLabs approach to custom homebuilding at scale can be used not just for upping the values of already fabulous homes, but also addressing the affordable housing crisis on Long Island. He’s met with East Hampton town officials about how to streamline the process of getting permits to build an ADU. “We want to create quality, custom homes for a wider market, not just the one percent,” says Chugh.
And as an immigrant-owned business, the co-founders are extremely intentional about how their company supports the community. For instance, Chugh says they’ve chosen to be the official sponsor of the Bay Street Theater for 2024-2025 because “architecture and art are inseparable in the Hamptons.”
Says Chugh, “It’s a natural fit; Bay Street enriches the East End with original performances, mirroring our dedication to enhancing local architectural beauty in a sustainable way.” Gupta has her own reasons. She says that the theater “walks the walk” when it comes to making the arts and leisure accessible to all, from Bay Street’s Pay What You Can Program, to its No Camper Turned Away summer series for children.
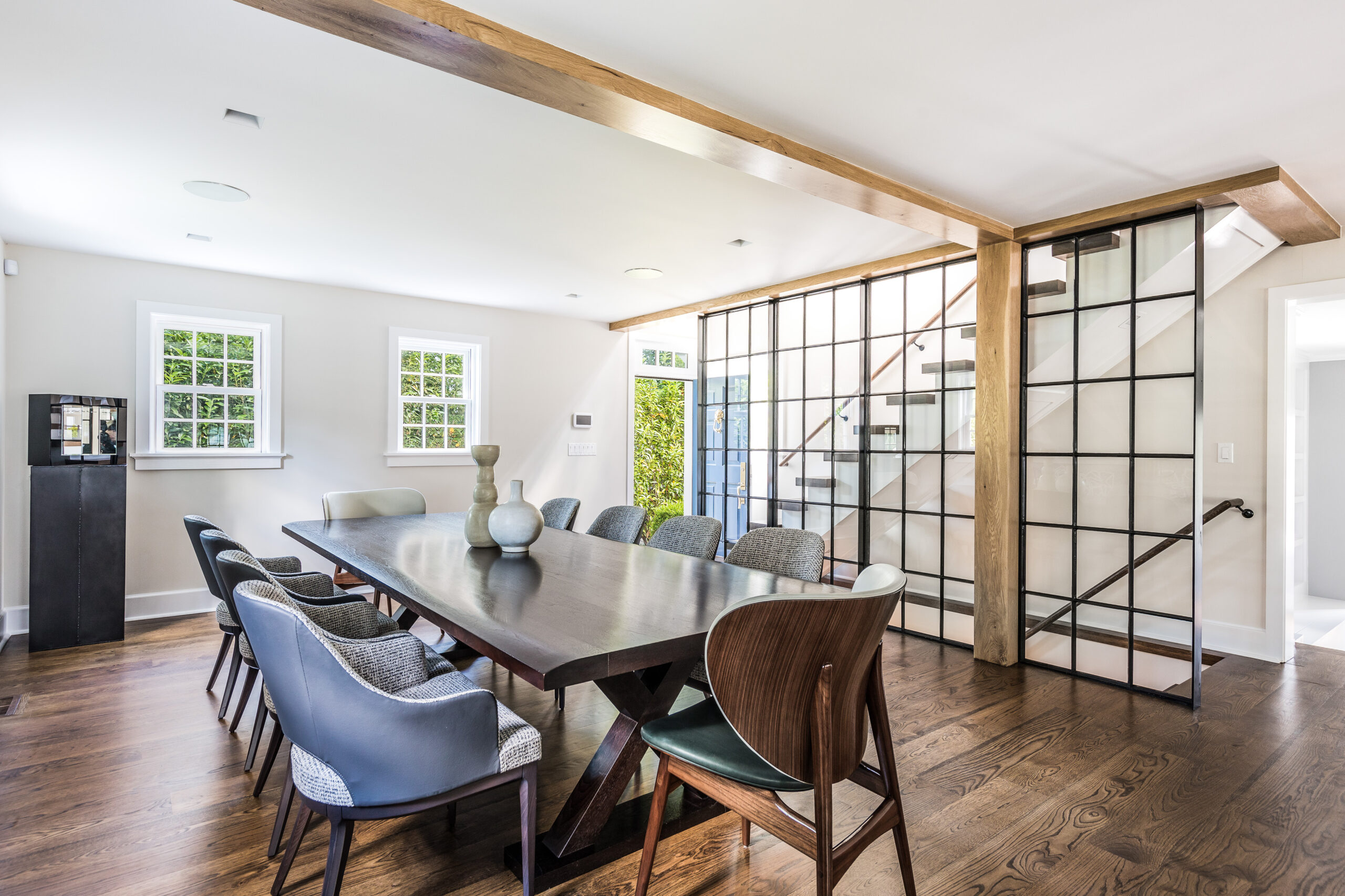
“BuildLabs’ support for Bay Street Theater is really support for the entire East End,” says Paul Anthony Mongelluzzo, sponsorships director at Bay Street Theater. “The partnership helps us achieve our mission to innovate, educate, motivate and entertain the diverse communities we serve all across the Hamptons and beyond.”
For the cofounders, it’s how they lead outside of the sleek glass-clad offices that count most, especially as their two college-bound sons, Aryan and Aman, help out their parents during peak construction season. Gupta, for example, acts as the unofficial sports photographer for the local school district whose students come from a broad range of socioeconomic backgrounds. “I do this for the kids, mine and theirs” she says, cherishing the bonds formed with students whose working parents are not always able to attend games.
But BuildLabs is ready to take on new terrain. This spring the company announced its goal to bring German building methodologies to US soil for the first time–and earlier this month, commissioners from Nash County, North Carolina approved BuildLabs’ plans to build a 60,000 square foot plant at its business park.
“This is just phase one of development,” says Chugh. “From expanding to the Mid-Atlantic to focusing on ADUs and our online configurators, we’re very much a tech-driven venture, with roots in the Hamptons.”
For more information, visit buildlabs.com.
Edited by Tanya Klich